氮化处理是指一种在一定温度下一定介质中使氮原子渗入工件表层的化学热处理工艺。经氮化处理的制品具有优异的耐磨性、耐疲劳性、耐蚀性及耐高温的特性。本期主要说说钢铁零件表面氮化那些事儿……
氮化工艺是在20世纪初期开发出来的,目前在很多工业应用都在继续发挥重要作用。它已经发展成为一种非常重要的表面强化工艺方法,氮化通常用于:
■ 飞机
■ 轴承
■ 汽车部件
■ 纺织机械
■ 涡轮发电系统
虽然它还包裹着一点点“炼金术的神秘”,但它仍然是最简单的硬化技术。氮化过程的秘密在于它不需要从铁素体到奥氏体的相变,也不需要从奥氏体到马氏体的进一步转化。换句话说,在整个过程中,钢可以始终保持着铁素体相(或渗碳体,取决于合金成分)。
这意味着铁素体(体心立方晶格或bcc晶格)的分子结构不需要不改变或转变成奥氏体的面心立方(fcc)晶格特征。在更为传统的渗碳方法中却需要晶格特征的转变。此外,因为仅发生在自由冷却,而不是快速冷却或淬火,所以不发生随后从奥氏体到马氏体的相变过程。
再次,没有分子尺寸变化,更重要的是,没有尺寸变化,由于氮扩散引起的钢表层体积只有轻微变化。在氮化过程中,产生的变形是由热量释放诱导产生的表面应力,引起了扭曲和弯曲形式的运动。
氮化是一种将新生氮扩散到钢和铸铁表面的铁素体热化学方法。这种扩散过程主要依赖于氮在铁中的溶解度,如铁-氮平衡图所示(图1)。
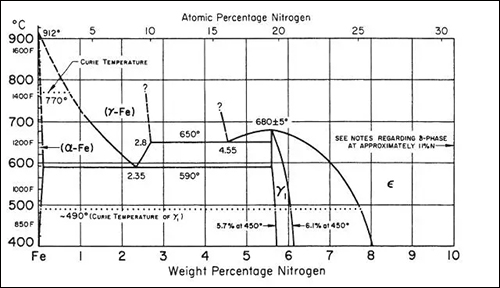
图1 铁氮平衡相图
氮在铁中的溶解度极限是具有温度依赖性的,在450℃(840°F),铁基合金将吸收高达5.7%至6.1%的N。除此之外,合金钢表面相的形成主要倾向于是ε相。
氮在的溶解度受钢中含碳量的强烈影响:一般来说,碳含量越大,形成相的可能性越大。当温度进一步增加到490℃(914°F)的γ‘相形成温度时,溶解度的“窗口”或极限在大约680℃(1256°F)的温度开始下降。
平衡图显示控制氮扩散对于氮化工艺成功是至关重要的(如图1所示)。必须遵守和控制多个操作过程参数以便成功地执行氮化工艺。大多数工艺参数可以用相对简单的仪器和方法控制。
用于气体氮化的工艺参数包括:
炉温
过程控制(见下面的讨论)
时间
气流
气体活度控制
过程室维护
除了引起的残余应力以外,所有这些因素都有助于减少工艺中的变形。氮化的另一个好处是,它可以对钢提供额外的回火处理作为稳定工艺。
工艺参数的控制是非常重要的,目的是获得良好的表面冶金状态。没有有效地工艺控制就不能保证冶金质量的可重复性。
工艺控制参数是确保氮化受控并且结果可接受的重要因素:
氮化总表面积
密封处理室内气相压力
气体输送压力系统进入密封处理室
来自密封处理室的废气系统
氮化前控制预热处理程序,包括应力消除,预硬化和回火
氮化前钢表面预处理的质量和完整性
一致的钢化学特性,最大限度地“氮化”
在20世纪初,Adolph Machlet在新泽西州伊丽莎白的美国天然气公司工作,担任冶金工程师。他认识到由于在高温下延长时间,接着严重淬火不管是水还是油,渗碳表面硬化技术都可能导致产生变形问题。
通过实验,Machlet很快发现氮极易溶于铁。氮扩散在铁或低合金钢中产生相对硬的表面,并且显著改善耐腐蚀性。这是在不使钢经受高温的情况下完成的,更重要的是,不需要使钢快速冷却以获得硬的耐磨表面。它现在可以在处理室内自由冷却,同时仍然在氮基气氛的保护下,从而降低变形的风险,但仍然可以产生耐腐蚀性良好的硬质耐磨表面。
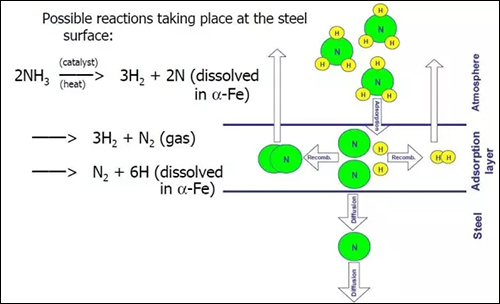
图2 氮化过程化学反应
在氮化的过程中,氨通过热分解或“裂化”以释放该过程所需的新生氮。不久以前,Machlet意识到他需要精确地控制氨的分解。他通过使用氢气作为稀释气体来减少可用的新生氮的量,从而在一定程度上控制的表面冶金来实现。工艺气体控制背后的理论基础是人们现在被称为“白层”或“化合物区”的认识。图3示出了氮化层的简单结构。应当注意,该示意图不是按比例绘制的。
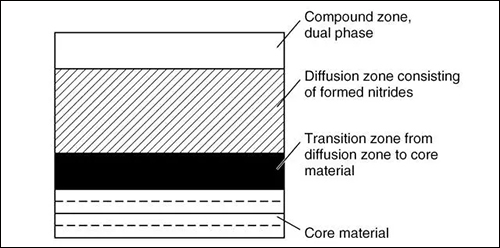
图3 氮化层结构简单示意图
涉及氮化工艺的第一个专利出现在1908年3月,在新泽西州伊丽莎白市申请。该专利最终在初始申请后约第五年,于1913年6月被批准。Machlet在他的专利申请之前已经进行了多年的工作,并继续开发新工艺和强化他对获得工艺冶金过程的理解。该专利是“在引入过量氢气的氨气气氛中钢铁的氮化”。
虽然Machlet的新渗氮工艺的开发和专利在技术上很重要,但他的工作仍然很大程度上未被广泛认识。即使在今天,也很少有渗氮专家知道他是谁,他完成了什么。大多数熟悉氮化过程的冶金学家都知道德国研究员Adolph Fry的工作,他被公认为“氮化之父”。虽然Fry的工作更多地被公开,他的方法在许多优秀的冶金学术研究机构都有讲授,然而,Machlet才是氮化工艺的真正先驱。
在德国,Adolph Fry在埃森的克虏伯钢铁厂正在进行一个平行研究计划。这个程序由Dr. Adolph Fry在1906年领导。像Machlet一样,Fry认为氮在高温下非常易溶于铁。他在工作早期也认识到合金元素强烈影响氮化的冶金和性能结果。在第一次世界大战结束三年后,弗雷1921年申请了他的专利。他的专利于1924年3月批准。
他使用类似于Machlet的技术,其中氮源必须通过热裂解以释放氮用于反应和扩散。像Machlet一样,Fry使用氨气作为源气体,但他没有使用氢气作为稀释气体。因此开发了如今已知的单级气体氮化工艺。
然后,Fry研究了合金元素对表面硬度的影响。他发现,氮化工艺仅在含有铬、钼、铝、钒和钨的钢上产生高的表面硬度,所有这些都形成了所谓的“稳定的氮化物”。
他还发现了工艺温度在表面氮化深度和表面冶金质量方面的关键影响。在较高温度下处理钢使得表面存在产生“氮化物网络”的风险中。
因为具有较高合金含量的钢不容易用于氮化,Fry负责开发被称为“Nitralloy”组的用于Krupp的一组钢。这些钢,特别设计为氮化钢,很快成为国际公认。
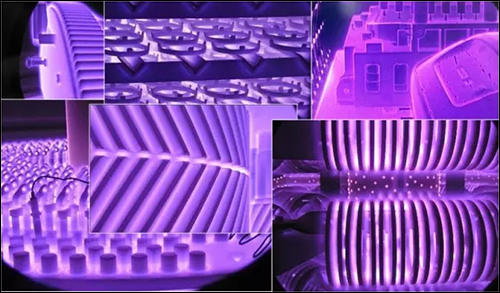
图4 齿轮等构件的氮化处理
此后不久,在20世纪20年代末,一家位于英国谢菲尔德的公司也开始在克虏伯钢铁有限公司的指导下开发一组氮化钢。这些钢也以Nitralloy品牌名称销售。该公司是Thomas Firth和John Brown Steelworks,更常被称为Firth布朗钢。来自Firth Brown的钢被称为“LK”组,由英国标准970指定为En 40A,En 40B,En 40C,En 41A和En 41B。为氮化应用开发的这些是铬-钼钢(化学成分见表1)。
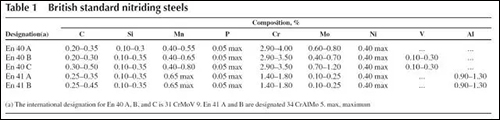
En 41系列含有铝,氮化后产生更高的表面硬度。铝对氮具有强的亲和力,形成非常稳定的非常硬的氮化铝,其量高达1.0%Al。远超过1.0%以后,铝对氮化后的表面硬度没有影响。
美国和德国进程之间存在一定的差异。美国与德国的方法之间的主要区别是:
美国工艺使用氢气作为稀释剂气体来控制气体和钢的氮化势,这又控制了最终的表面冶金质量。
德国人通过合金化操作该工艺,并在核心硬度和抗拉强度等方面进行改进。
Machlet的工艺在美国没有被广泛接受,因为它被认为对美国工业没有什么商业价值。相比之下,德国人在第一次世界大战后的早期就利用了Fry的工艺。在整个欧洲,德国工艺在飞机、纺织、铁路、汽车和机床行业获得巨大成功。
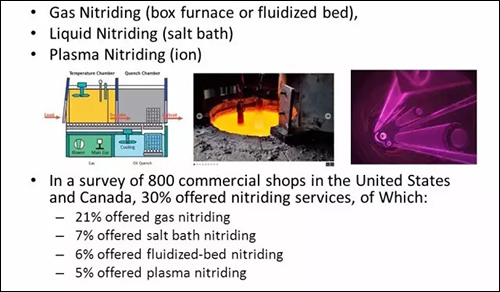
图5 常用氮化工艺方法
在20世纪20年代中后期,关于Fry的成功的消息开始影响到美国工业家,促使制造工程师协会(SME)对德国的氮化工艺的发展产生了浓厚的兴趣。
Zay Jeffries博士从俄亥俄州克利夫兰来到德国,于1926年访问克虏伯钢铁公司和Fry博士。正是在这次会议上,杰弗里斯建议Fry,他参加即将在芝加哥举办的年度中小企业会议,并介绍论文中的工艺技术和应用。Fry不能出席,所以他的朋友和同事皮埃尔·奥贝尔代表他做了一个演讲。该演讲促进了氮化工艺在美国的商业化。
更多关于材料方面、材料腐蚀控制、材料科普等方面的国内外最新动态,我们网站会不断更新。希望大家一直关注国家材料腐蚀与防护科学数据中心http://www.ecorr.org