1 前言
据统计,2016年我国已实现汽车销量2794万辆,同比增长 14.1%,其中,乘用车销量为 2 429 万辆,同比增长15.1%。随着国内人均乘用车保有量的逐年递增,客户对整车性能属性需求也越来越高;其中整车防腐属性涉及到整车性能、整车外观、车身结构强度、零部件的功能及可靠性等,因此,如何规范零部件表面处理、车身防腐设计、工艺防腐设计;如何验证和评价整车防腐性能一直是各整车厂制定企业标准的重点工作。
国外整车强化腐蚀试验及评价方法起步较早,同行业比较认可欧系、美系和日系的评价方法,其中 Volvo 最具有代表性。目前,我国现有整车强化腐蚀试验是 Q/CT 732《乘用车强化腐蚀试验方法》,试验故障以腐蚀严重程度区分,用10级标准来评价,评价结果较为抽象。为了便于试验结果对比分析,提高整车研发工作质量和效率,研究分析了以下5个评价维度,将每个腐蚀故障、整车防腐性能及整车性能扣分均转化为量化的评分数据。
a.故障管理:故障分类、故障代码编制方法。
b.故障评分方法:评分方法(10分制)、故障评分细则、故障评分节点。
c.评价者培训:评价者资质培训、评价工作组织实施。
d.整车评分:系统故障评分加权系数、整车防腐性能评分计算公式、整车扣分计算方法、整车防腐性能最终评分计算公式。
e.腐蚀年限(星级)评价:乘用车腐蚀年限预测、乘用车5星评价制。
2 故障管理
2.1 故障分类
在 QC/T 900 可靠性故障分类基础上,结合整车腐蚀试验特点、金属及非金属材料腐蚀特性,将试验故障等级分为四类,并分别给予定义和结果判定。故障分类是该综合评价体系的基础,也是判断整车腐蚀试验合格与否的依据。“故障分类”细则见表1。
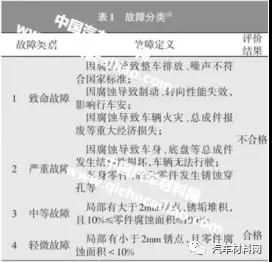
2.2 故障代码编制方法
故障代码需具备规范性、完整性、唯一性和可查询性,便于准确、快捷从数据库中查询。故障代码编制规则见图1。
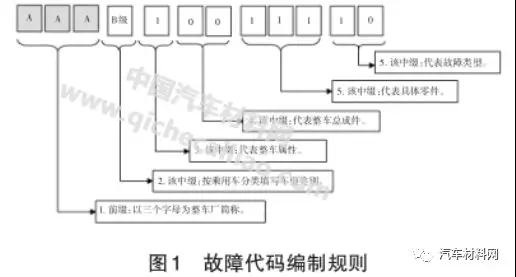
a.评分 10 分制,得分越高,该零件防腐性能越好。
b.评价依据评分细则。
c.顾客满意度在开发阶段,从用户角度分析并预测整车上市后的用户满意度。
d.评价者在开发阶段,由防腐工程师、设计师、项目组、售后等团队成员共同参与评价。
e.故障类型与“故障分类”对应。
f.评价结论,如果故障评分小于等于3分,整车防腐性能不合格;同时,不计入评分。如果故障评分大于等于4分,整车防腐性能合格;并纳入该文的评分方法。
3 故障评分方法
3.1 整车腐蚀试验故障主观评价(10分制)
在乘用车强化腐蚀试验过程中,当试验样车出现锈蚀故障时,第三方机构或厂家工程师一般都用文字描述,或测量腐蚀区域的长度、宽度,并附带故障照片,反馈给设计师;对有经验的防腐工程师或设计师,根据整车防腐属性设计要求、反馈的定性信息、以及试验周期与市场腐蚀年对应关系,能判断该故障的整改等级;反之,工程师将无法判断故障的严重性,也无法对故障整改等级做出合理判断。
为突破这一瓶颈,根据国情并结合国外评价方法,制定了“整车腐蚀试验故障评分方法”,见表2。
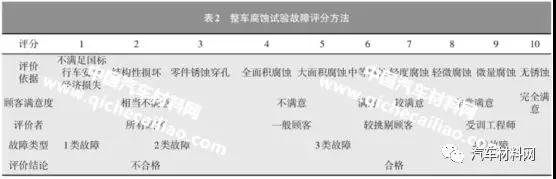
3.2 故障评分细则
对每个腐蚀故障评分依据,参照表3故障评分细则。
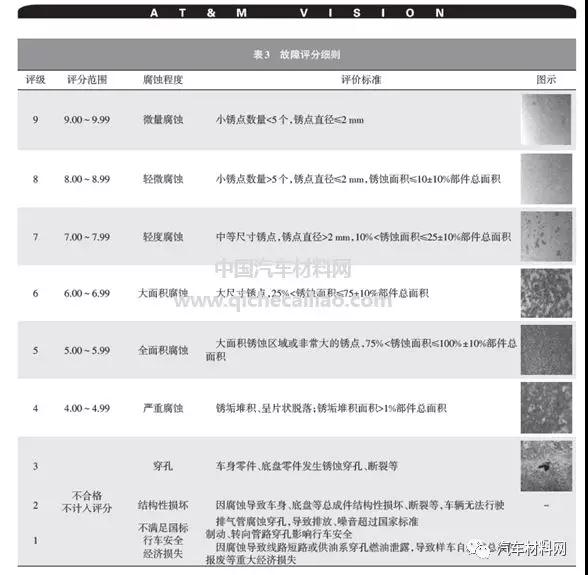
3.3 故障评分节点
腐蚀故障评价包括以下两个部分。
a.整车腐蚀试验过程中,根据整车防腐属性定义的不同,制定对应区域的零件签收节点,见表4故障评分签收节点。
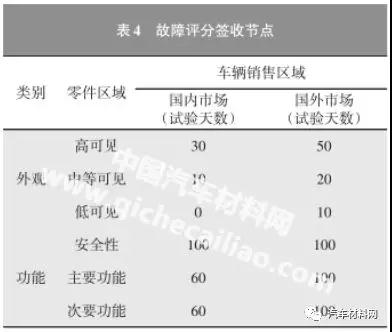
在腐蚀试验中,凡是签收节点内发生表面出现锈蚀的零件,都属故障评分范围;故障计分后需按车身、附件、底盘、发动机、电器和内、外饰进行分类。
b.试验样车拆解后,故障评分方法与试验过程中一致;故障零件除锈后,测量零件厚度减薄率或重量减少率,并计算剩余寿命,已评价该零件是否满足零件的防腐设计要求。
4 评价者培训
4.1 评价资质培训及实施
评价者入门资格要求为三年以上腐蚀试验相关工作经验,专业要求为汽车专业或材料。评价者培训课程如下。
a.汽车构造及原理。
b.汽车制造工艺,包括冲压、焊装、涂装及总装。
c.乘用车强化腐蚀试验方法。
d.评价方法:评分方法(10分制)、故障评分细则、故障评分节点内容。
e.故障评分方法:整车防腐性能评分计算公式、整车扣分计算方法、最终评分计算公式。评价者考核方法如下。
a.随机选用 30 个腐蚀故障做为样本量,由评价者进行评分。
b.用 6-Sigma 的肯德尔系数(Kendall's Coeffi-cient Of Concordance)计算评价者评分的一致性。
c.用 6-Sigma 中的 Minitab 软件计算出 P 值、KCC值,考核要求为KCC值在0.7~1.0范围内,相关性高,可接受;KCC值越大,一致性水平越高;P值需小于0.05。
“Minitab软件计算方法”见图2。

4.2 评价组织实施
a.评价小组:2~3个。
b.每组评价人员:2~3人。
c.初期评价:每个评价者对每个腐蚀试验故障进行评价,得出故障评分值后,汇总所有故障的评分结果;小组内讨论每个评价者评分值的合理性,并得出小组的故障评分结果;小组之间讨论各小组评分结果,得出最终的评分结果。通过经验摸索,分析评分结果的规律性和合理性,制定公司程序文件。
d.中期评价:评价者按程序文件评价每个腐蚀试验故障;对难以评价的试验故障,小组内、小组间进行讨论,并确定最终评分值。
e.长远目标:定性、定量每个试验故障,运用软件或腐蚀仿真计算后,得出评分结果。
f.基本原则:对不满足国标、整车自燃、总成件损坏、转向/制动/燃油系统失效、结构性损坏、零件锈蚀穿等评分值低于3分的故障,需团队进行讨论后确认;对评分值高于9分的故障,也需团队进行讨论后确认。
5 整车评分
5.1 系统故障评分加权系数
根据2010至2014年汽车质量网信息,分析了26家整车企业腐蚀缺陷抱怨信息,按乘用车系统进行分类、统计故障率分布。26家整车企业整车腐蚀缺陷分布(2010~2014)见表5。
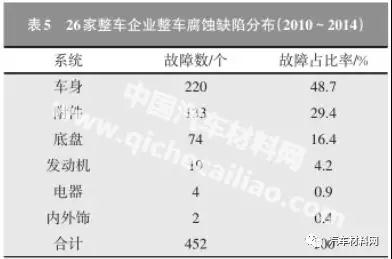
根据市场腐蚀缺陷抱怨的故障占比率分布,并依据乘用车腐蚀试验特点、用户关注度等要点,即腐蚀试验验证重要度、以腐蚀工况验证强度、以零件安装区域(高可见度、中等可见度、低可见度)、从整车性能重要性。制定系统故障评分加权系数,见表6。
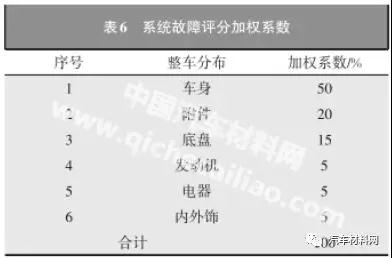
5.2 整车防腐性能评分计算公式
按照表3,故障评级为1级、2级、3级,即属于1类故障和2类故障;整车防腐性能评价为不合格,同时,不计入下述公式进行故障评分。
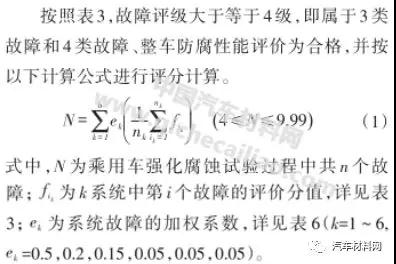
5.3 整车扣分方法
整车强化腐蚀试验扣分目的如下。
a.整车强化腐蚀试验是验证整车防腐性能是否满足技术规范和市场需求。
b.整车强化腐蚀试验结束后,试验样车性能衰减直接影响用户满意度和品牌形象。扣分值定:整车总扣分率为10%,即1分;整车性能:0.5分;整车主观评价:0.5分。
整车扣分有两部分组成。
a.客观测量值:整车性能复试的衰减率大于等于性能初试的10%;按表7的“整车性能扣分方法”扣分方法进行。计算方法,见公式2。
X1=25%×(S1+S2+S3+S4) (0≤X1≤0.5) (2)若单项衰减率大于35%,则X1计算为0.5分。
b.主观评价值:整车操稳、NVH、电器性能、可维修性的复试衰减率大于等于初试的10%;按表8的“整车主观评价扣分方法”方法进行。计算方法,见公式3。
X2=30%×S1+30%×S2+30%×S3+10%×S4(0≤X2≤0.5)(3)若单项衰减率大于35%,则X2计算为0.5分。
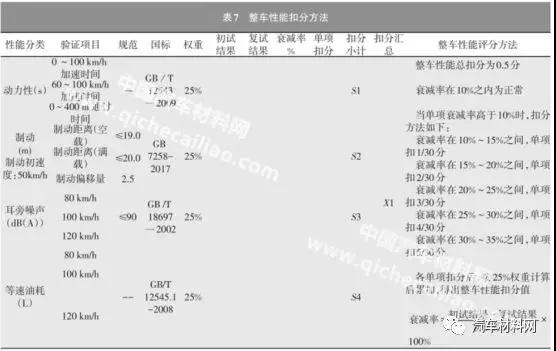
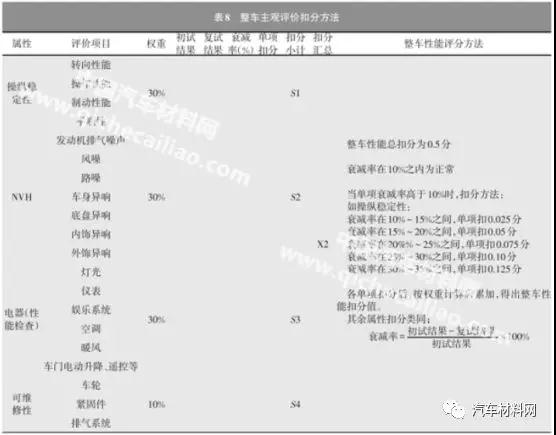
5.4 整车防腐性能最终评分计算公式
根据整车防腐性能评分方法及整车扣分方法,整车防腐性能最终评分S的计算公式如下,见公式4:
S=N-X1-X2 (4≤S≤9.99) (4)
6 腐蚀年限(星级)评价
6.1 乘用车腐蚀年限预测
目前国外乘用车最高防腐要求:6年外观无腐蚀、12年零件不穿孔、12年功能性无失效、12年可维修性;同时分析大量的整车强化腐蚀试验结果,结合国内、外市场防腐抱怨的分析结果,对乘用车腐蚀年限做了预测,前提条件是该乘用车的强化腐蚀试验需要用该论文的评价方法。乘用车腐蚀年限预测见表9。
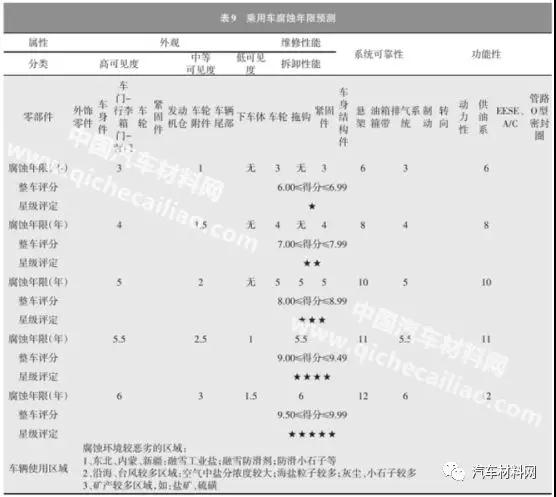
6.2 乘用车5星评价制
在乘用车腐蚀年限预测的基础上,以国际整车防腐性能最高标准为依据,结合美系、日系车的评价方法;同时参照国内市场的腐蚀抱怨数据,预测乘用车5星评价制,见表10。
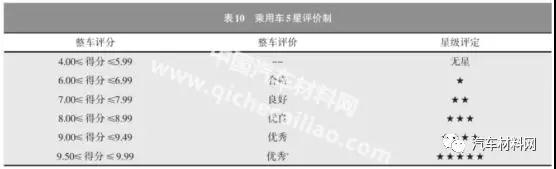
7 总结
a.建立了完善的乘用车强化腐蚀试验评价体系,用量化数据评价试验故障,制定了系统的权重评分系数,同时按整车性能及主观评价衰减率扣分,最后得出乘用车防腐性能的得分值。
b.定性、定量的试验故障评价方法,有利于试验故障整改,提高开发设计质量。
c.有效、合理降低不同评价者的主观评价差异,确保评价结果的重复性和再现性。
d.在国内首次引入“乘用车腐蚀年限预测”及“乘用车5星评价制”,为建立国内的乘用车防腐性能5星评价制,提供了思路和依据。